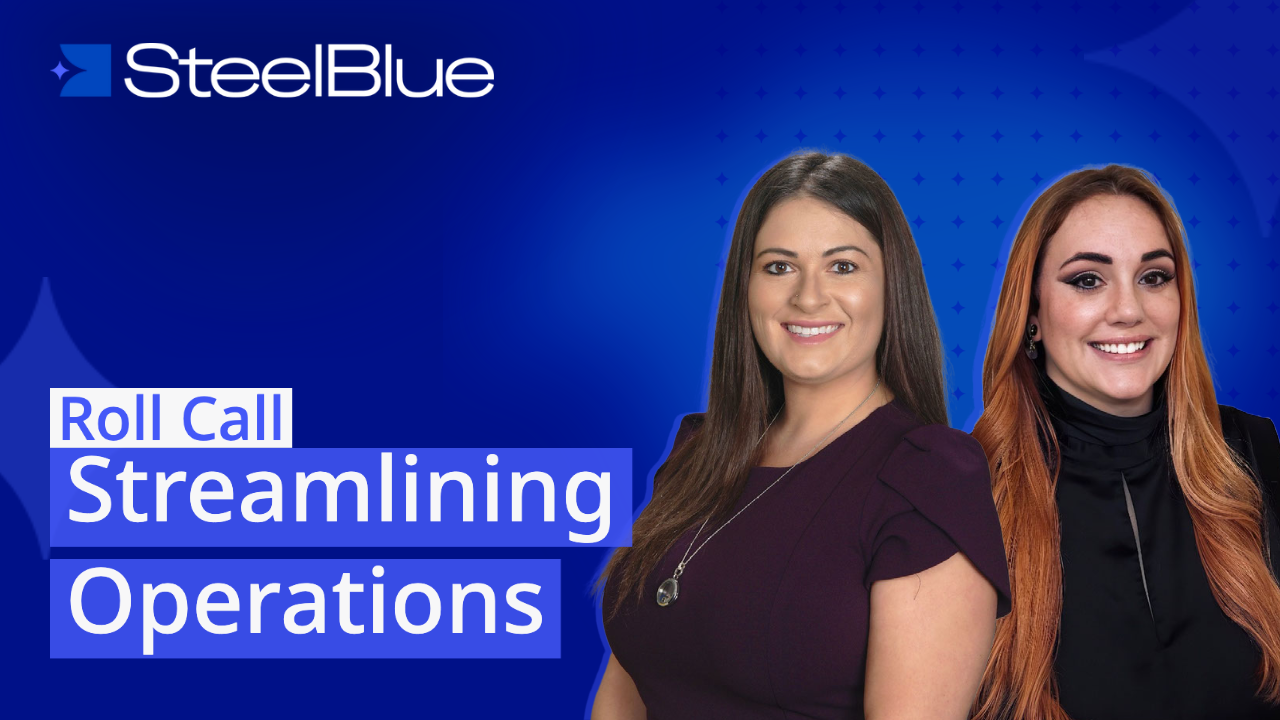
Roll Call: Streamlining Operations
Scheduling operations and logistics are the backbone of any business that involves manufacturing or transportation. When it comes to the door industry, it is no different. However, with the fast-paced nature of manufacturing and shipping, it can be challenging to stay on top of everything.
That's why we sat down with two of our in-house experts, to learn more about how they streamline scheduling operations and logistics to improve efficiency, reduce waste, and keep customers satisfied.
So who are these subject matter experts?
First was Sydney Hogan, our Director of Transportation. Sydney has been with us since the very beginning. She has witnessed and played a key role in helping us grow into the company we are today.
Sydney is a seasoned professional with over 16 years of leadership experience in procurement and warehouse management, acquired through various manufacturing positions. Her background and experience make her a valuable subject matter expert in the areas of production and logistics, transportation, and supply chain management.
We also spoke to Sierra Smith, our Production Scheduling Manager who joined us as we really started to hit our strides as a company as we were improving our manufacturing capabilities on a daily basis at the time of her arrival. Her 10+ years of experience in production scheduling makes her an ideal expert for this conversation.
But, what did we talk about?
Streamlining Scheduling Operations
Streamlining scheduling operations means making the process more efficient by identifying and eliminating waste. Sierra and Sydney both agree that having a reliable and up-to-date schedule is critical. It allows for better communication among team members, reduces errors, and ensures that projects are completed on time so that our customers can thrive.
They recommend leveraging technology, such as our upcoming ERP system, to automate the process and reduce the risk of human error. Despite technology playing a huge role in the future of their work, they emphasized the importance of human connection at work and how vital that is to executing as a team.
Optimizing Logistics
In the door industry, logistics can be a complicated process that involves a lot of moving parts, especially in recent years. However, Sierra and Sydney stress that it is essential to optimize logistics to ensure that customers receive their orders on time and in pristine condition.
They recommend establishing clear communication with truck drivers and customers, setting realistic delivery expectations. Also, they suggest that it is crucial to consider the unique challenges of each delivery location, such as difficult-to-navigate roads, and plan accordingly to ensure that deliveries are made safely and efficiently.
Despite all of this preparation, you have to expect the unexpected and act quickly. There are so many working parts in this chain that can go wrong and it takes a unified team to work together in order to ensure that we can make good on our commitments to you, even in the toughest scenarios.
Creating a Culture of Excellence
It was evident in our conversation that our team at SteelBlue lives our core values from top to bottom as an organization. The value of Collaboration comes up time and time again whether you are talking to executives or people from day to day operations. Everyone is on board with working together, wearing multiple hats in true startup fashion to ensure the success of our customers.
Another core value that shines through during this talk is Transparency. Anyone on our team has access to anyone in the company, especially our leadership team, whenever they are needed. Nobody is hiding behind any corporate veil here, we are an open book and welcome your questions at any time during our work together.
The Last Word
Streamlining scheduling operations and logistics is a complex process that requires constant evaluation and improvement. Sierra and Sydney provide valuable insights into how they approach these challenges to keep our customers happy and their operations running smoothly.
By following their example, businesses in the door industry and beyond can improve efficiency, reduce waste, and provide better service to their customers while maintaining a work environment that allows everyone to prosper.